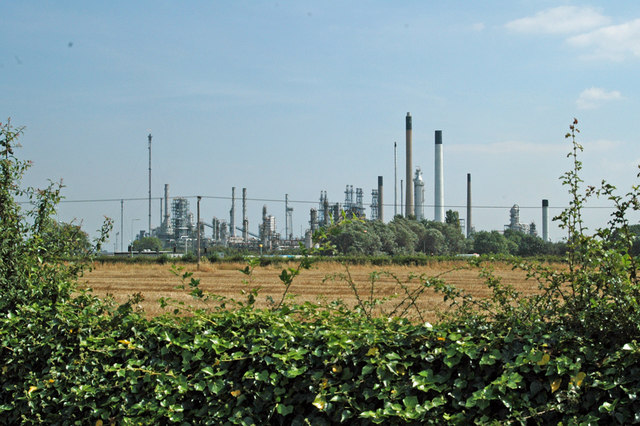
Piping Technology and Products has a unique perspective on best practices in preventative maintenance. PT&P has a database built from over 1,000 audits performed in 41 countries. PT&P also has experience from over 3 Million pipe supports and expansion joints currently in service.
The following is a summary of the strategies PT&P sees at operating plants:
- Only fix spring supports when something is wrong (e.g. vibration, leaks, …)
- Perform regular inspection and replace damaged spring supports
- Periodically return piping line to its original design specification and/or set new design standard if the design has changed
The design of the piping system is a major part of the engineering of an operating plant build. On average, piping constitutes 40-48% of the engineering hours in a new refinery. The challenge facing piping engineers is rotating equipment locations and process design are defined and the piping engineers must make the piping system fit within the designated space while dealing with thermal stress, proper flow, and allowable loads for all equipment. With temperatures in high energy lines often well over 1,000 degrees, this can be very challenging. The following are some of the goals of pipe stress engineering and the placement of spring supports and expansion joints in the piping system:
- Ensure stress at the interface to moving equipment is below maximum allowable loads
- Minimize turbulent flow through the piping system
- Ensure the longevity of piping system components
Figure 1 – Pipe Support and Expansion Joint Maintenance Strategy
*Shows the strategies that PT&P commonly sees at different operating plants:
Strategy | Pros | Cons |
Fix When Broken |
|
|
Periodically Fix Broken Springs (Component Level Focus) |
|
|
Periodically Return to Original Design Specification (System Level Focus) |
|
|
PT&P has seen many examples of each of the strategies above. Typically, the strategy taken at an individual plant is closely related to overall operating philosophy of the organization, including finance. However, we also speak to a number of organizations who have placed an emphasis on preventative maintenance but are not sure of the best practices for the engineered pipe supports and expansion joints.
Appendix A shows an example of a program PT&P executed March of this year on a turnaround. For preventative maintenance, best practice is to not just focus on the health of the piping system components, but on the health of the overall piping system. The following are some of the issues that PT&P has found that cause system level issues:
- Spring Support Failure Impact – the failure of a spring support will impact other supports and cause them to possibly fail as they attempt to take on the additional load of the failed spring
- Damage to Piping or Rigid Supports Changes Elevation of Spring Supports – a variety of issues can cause the piping to undergo strain, which causes deformation. This will cause a change of elevation or distance from the pipe support to the pipe and impact the load setting and connections to other equipment
- Improper Travel Stop Management – if travel stops are not removed, the spring supports are essentially a rigid support, and the load can be redistributed among the spring supports on the same line in a way that is not consistent with the original design
- Improper Initial Installation – one of the most common issues PT&P finds in its audits is that engineered supports are improperly installed during initial installation
By the time a plant reaches 10+ years of age, PT&P’s experience is that most plants have encountered one or more of the issues above. For this reason, it is essential to take an approach of resetting the line to the original design specification. Best practices for performing a “reset to design specification” are the following:
- Hot and Cold Audit – required to understand the range of movement
- View of Functioning of Springs/Expansion Joints Across Line – the view of how a spring is functioning can be highly dependent on whether there are many failed supports on the line versus just one
- Plan for Adjustments and Replacements – the overall plan for a turnaround must be comprehensive in terms of adjustments
- Proper Management of Travel Stops – we have found tremendous confusion on the proper timing for placement of travel stops; if this is not done correctly, in many cases it is not possible to reset the line to the original design specification
- Repair Rigid Support Issues – a common issue we have run across is a damaged or removed pipe shoe or saddle resulting in the piping sitting on the supporting pipe rack
- Assess Elevation Changes – changes in elevation due to changes or deformation of piping can cause a spring support to be out of position; this issue should be addressed as an issue with the line rather than the spring support
- Identify Design Changes – PT&P sees many situations where there have been alterations to the line, such as new equipment without an update of the stress analysis; the best approach is to redo the stress analysis; however, the budget or time constraints may require a quick and dirty approach such as weighing the line
- Adjust in Real Time as Needed – Given all of the issues above, resetting a piping line to design specification takes real-time decision making during an audit
The challenge with this approach to preventative maintenance is that it takes a much deeper level of expertise than a component level inspection. PT&P’s experience is that even the ability to operate a pipe stress modeling software program such as CAESAR is far different than a pragmatic understanding of the proper functioning of all the elements of the piping line. Many personnel and firms supporting piping system maintenance are challenged with managing a broad range of equipment at an operating plant, and this can make it difficult to have the depth in pipe stress that may be required to properly execute a system level audit and execute a plant to return the piping system to the original design specification.
The sole purpose of performing audits is to maintain the piping system and equipment to remain in the proper condition. Therefore, the system level (pipe stress audit) that considers the physical condition of the system, along with the spring supports system should be preferred. As mentioned earlier, the component level audit is an important part of the system level which if put together with other system and/or deformation assessment can give the overall picture of the system and finally a better direction for the proper maintenance.
An Example of System Level Repair Work: Spring Supports Issues on Manifold of a Heater
PT&P performed an installed inspection on all the springs supporting a manifold of a heater. The installed (or ”cold”) condition inspection showed that most of the supports were operating properly. However, after performing a second inspection in the operating (or ”hot”) condition, it was concluded that most of the spring supports did not show any signs of movement. This issue was brought up with the customer, and it was determined they were having some issues with the heater tubing affecting the efficiency.
![]() |
![]() |
During Cold Inspection | During Hot Inspection |
Since this issue needed to be addressed to prevent any failures in the future, all the supports from the manifold were assessed and concluded that there is a need for system level repair. Therefore, on a 2019 turnaround, all the spring supports of the manifold were replaced.
The following pictures show that the new supports are moving as designed and system-wide repair was indeed required.
![]() |
![]() |
During Cold Inspection (March 2019) | During Hot Inspection (May 2019) |
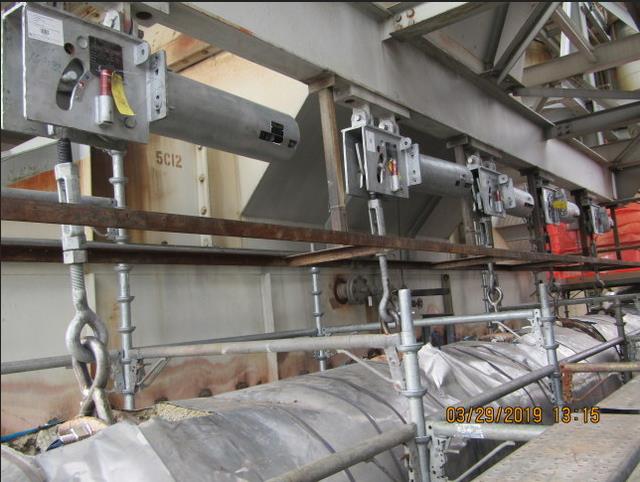
All together 35 spring supports on manifolds were replaced due to failure of previous spring supports.
Appendix A: Turnaround plan and Execution for a Major Refinery
|
|
Work Scope:
- Pipe supports inspection during the installed or cold condition
- Supervision on adjustment of the spring supports
- Installation of spring supports as per in Table A for the period of 30 days
In addition to the above, PT&P provided a supervisor (Expansion Joint Technical Expert) to supervise the installation of expansion joints.
Planning:
PT&P provided two engineers about a year before the turnaround to perform the operating inspection of the spring supports while a cold inspection was done by PT&P in the previous turnaround. All these inspected supports were documented in a report and the conditions were categorized as good, replacement or adjustment required.
Pre-Turnaround:
Based on the location provided in the inspection report, and constant communication between PT&P engineers and turnaround co-coordinators, the location where the scaffold is to be built was pre-planned.
The materials were purchased a few months before the turnaround. All the required safety training, drug tests, background checks were done prior to the turnaround date.
During Turnaround:
Out of 10 units, 4 units were “shut down” upon arrival at the site. PT&P engineers performed a quick walk-down on all the spring supports in the units to see if there were any new issues since the last inspection which required immediate attention. This gave enough time to order the materials and necessary hardware.
After the quick inspection, PT&P worked with a few client technicians on two different units. The adjustment and installation work on the two units were done concurrently.
Once those units were completed, PT&P engineers were mobilized to other units. There were a few new discoveries where PT&P engineers ordered materials for adjustment and replacement. Within a couple of days, PT&P managed to supply the parts (shipped through hot shot) and resolve the issues.
There were five times, PT&P provided the materials during the period of turnaround within 48 hours. It was very convenient to have engineers supervising the installation and repair as it allowed for design and/or engineering changes to be made on the spot.
In addition to the pre-planned turnaround work, PT&P engineers assisted, on several occasions, to help resolve issues such as bent struts, check the condition of counterweights (old style), some new expansion work which included the addition of new pipe supports.
Pictures of replaced cans:
![]() |
![]() |
Cracked Spring Support | After Replacement |
![]() |
![]() |
![]() |
Bent Rod During Turnaround Work | After Repair | During Follow-up Hot Inspection |
The rod was bent during the turnaround because the contractor working did not reinstall the travel stop while working with the line. The support should have been locked and disengage from the system for this specific work on the pipe coming out of the reactor. The line seemed to have higher movement than anticipated during the turnaround work. This was the second time the rod was bent. PT&P engineers, which were on site for other spring supports work, were contacted immediately. Less than an hour, PT&P field service technicians went and assessed the condition and suggested an improved, robust design. The materials were purchased as per PT&P engineers’ recommendation. Since the order came directly from the field from a PT&P employee, the approval and manufacturing process was smooth and quick. Within a couple of days, the materials arrived and were successfully installed. Everything operated correctly during the follow-up hot inspection.
For Expansion Joints (EJ):
PT&P supervisor was on site the entire time helping the contractor remove and INSTALL the new expansion joints. Almost all of the CLIENT contractor workers were inexperienced or very limited experience working with expansion joints.
PT&P supervisor gave a quick training about removing and installing the new EJs. They also pointed out the importance of being sensitive towards the EJ fabric since one small improper cut could damage the belt.
PT&P supervisor assisted the contractor with the proper marking of “backing bar” while removing the old EJ. He inspected the condition of the joint and guided contractors to efficiently install the new expansion joint. He also showed the proper way to splice the fabric materials to complete the EJ Installation.