Installation Steps
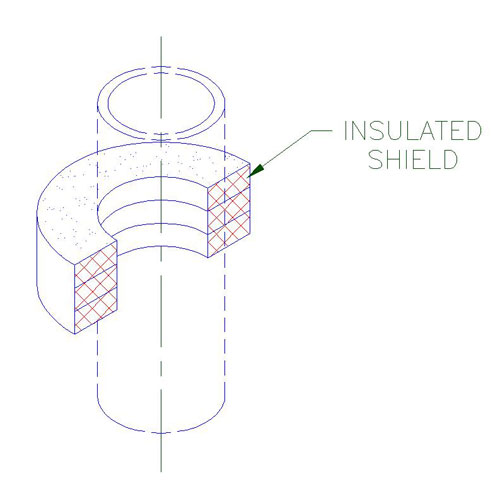
1. A) Position one half of the insulated shield (insulating structural material and sheet metal jacket) on the pipe at the desired location as shown.
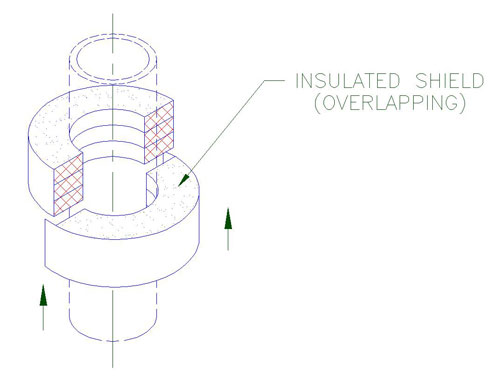
2. A) Gently slide the other half of the insulated shield with the overlapping jacket into position over the previously located half shield.
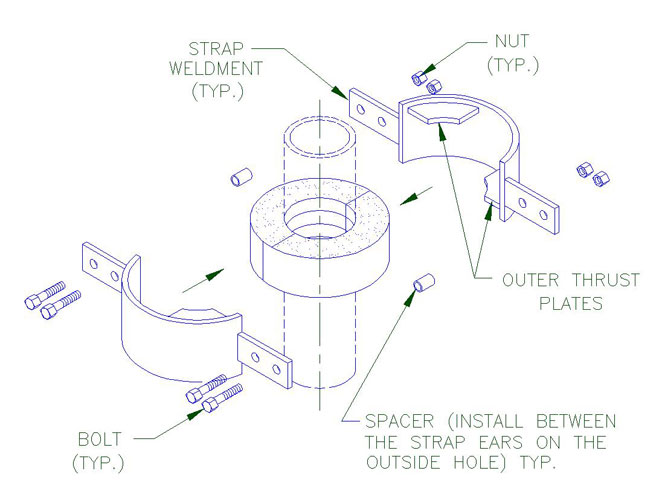
3. A) Assemble strap weldments (strap with shop welded outer thrust plates) and line up the bolt holes.
B) Install the bolts, spacers, lock washers and nuts as shown.
C) Hand tighten nuts before applying the specified torque.
D) Select torque value that correspond with the pipe size and model designation of the unit shown on Table 1. During tightening, it is recommended that the nut is turned rather than the bolt head and that the bolts be crosstorqued until the required torque has been achieved to obtain an even pressure on the structural insulation. To ensure that the bolts are properly crosstorqued by checking the spacing (B) between the ears to be approximately the same.
Note:
When models include heat trace groves, the number and location may vary. Check with design drawings for exact number and location. Ensure that the heat tracing cable is properly positioned inside the grove of the shield.
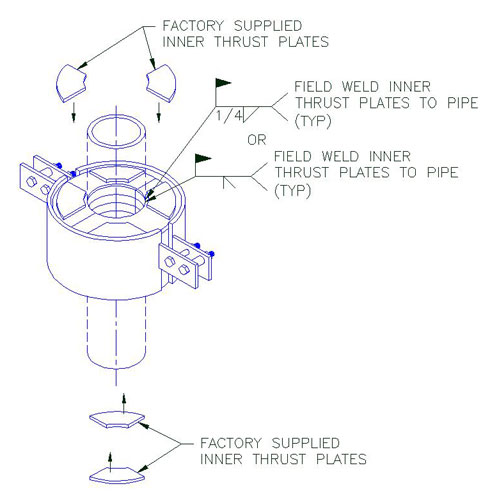
4. A) Locate and position factory supplied inner thrust plates (two on each side of the assembly) on the pipe. See below for locating and positioning the inner thrust plates on the pipe. When properly positioned weld them to the pipe as shown.
Note:
In order to act properly as designed, it is important that there is a zero clearance between the inner thrust plates and structural insert. It is recommended that the inner thrust plates be clamped tight against the structural insert before welding and remained clamped until the weld has completely colled-off to avoid or minimize shrinkage and/or distortion due to welding. If ther eis axial clearance, cut galvanied sheet metal shims to the same outline as the inner thrust plates and isntall them to reduce this clearance to zero.
Inner Thrust Plate Detail
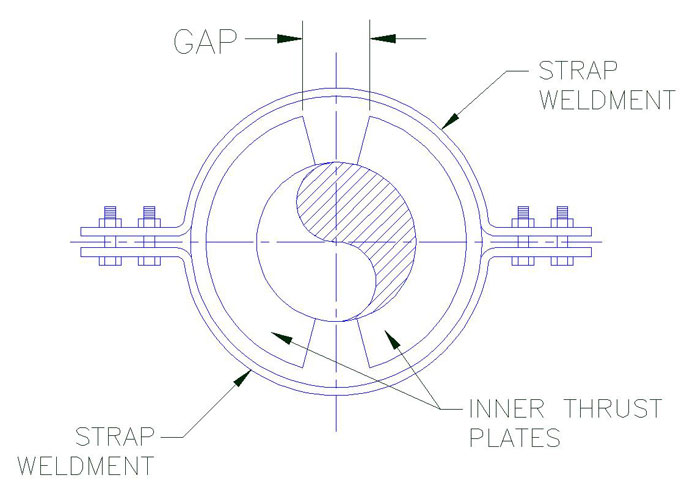
Section A-A
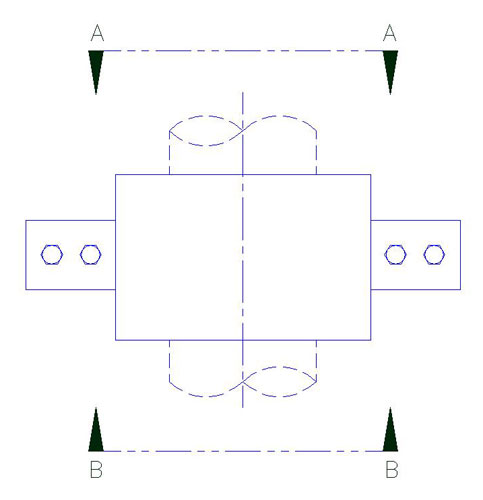
Elevation
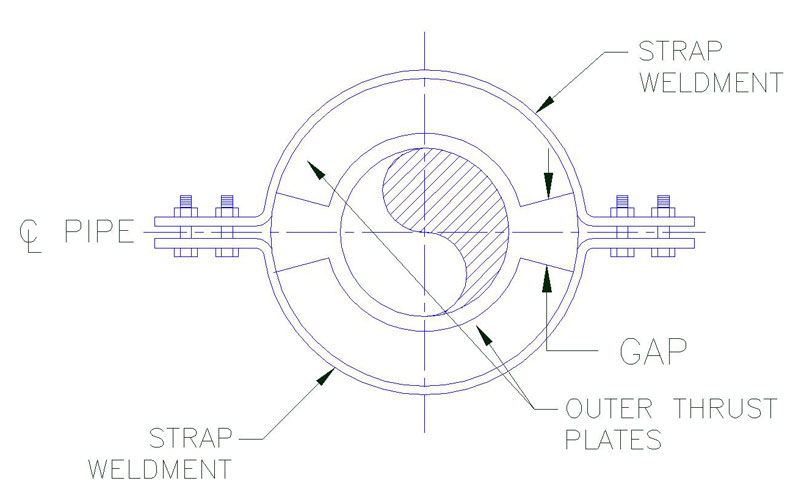
Section B-B
Notes:
1. Located the inner thrust plates on the side of the assembly directly opposite the outer thrust plates located on the
other side of the unit at all times (see sections A-A and B-B).
2. Position the inner thrust plate to provide equal clearance (*) between the edges of the inner thrust plate and the
two adjacent outer thrust plates as shown above.
* Gap tolerance
– 2 1/2″ thick insulation and less + 1/8″
– Greater than 2 1/2″ thick insulation + 1/4″
Table 1 Bolt Torque |
||||
Pipe Size | E2000 Series | E2100 Series | E2200 Series | E2300 Series |
Bolt Torque (FT-LBS) |
Bolt Torque (FT-LBS) |
Bolt Torque (FT-LBS) |
Bolt Torque (FT-LBS) |
|
1 | 3-5 | 3-5 | 3-5 | |
1.5 | 3-5 | 3-5 | 5-7 | |
2 | 3-5 | 3-5 | 8-10 | |
2.5 | 3-5 | 3-5 | 8-10 | |
3 | 3-5 | 8-10 | 13-15 | |
3.5 | 3-5 | 8-10 | 13-15 | |
4 | 3-5 | 8-10 | 13-15 | |
5 | 5-7 | 13-15 | 18-20 | |
6 | 6-8 | 13-15 | 23-25 | |
8 | 8-10 | 18-20 | 28-30 | |
10 | 13-15 | 28-30 | 43-45 | |
12 | 13-15 | 28-30 | 43-45 | 58-60 |
14 | 18-20 | 38-40 | 58-60 | 73-75 |
16 | 18-20 | 38-40 | 58-60 | 88-90 |
18 | 23-25 | 48-50 | 73-75 | 98-100 |
20 | 23-25 | 48-50 | 73-75 | 98-100 |
24 | 23-25 | 56-60 | 88-90 | 118-120 |