Installation Steps

1. A) Locate and position the restraint weld menton the steel support member as shown.
B) When properly positioned, weld the restraint weldment to support steel as shown.
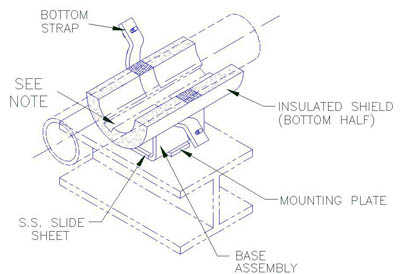
Model B1000 – B1300
Model: B2000-B2300
2. Position bottom half of the insulated shield into the base assembly. Ensure that the inserts are properly located over the straps by checking that:
A) Each end of shield shall have equal distance (c) from outer edge of strap (Figure A).
B) The 180° section of the bottom half shield shall be parallel to the support base (Figure B).
3. A) Slide the base assembly and bottom half shield under the pipe.
B) Position the base assembly on the restraint weldment to allow for anticipated axial travel.
Notes: When models include heat trace groves, the number and location may vary. Check with design drawings for exact number and location. Ensure that the heat tracing cable is properly positioned inside the grove of the shield.
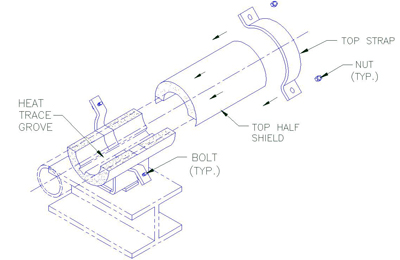
Model: B1000-B1300 Series
Model: B2000 – B2300 Series
4. A) Slide the top half shield into position above the bottom-half shield.
B) Gently place the top strap(s) into position above the bottom strap and line-up the bolt holes.
5. A) Install the bolts, lockwashers and nuts and hand tighten. For ease of bolt torquing, install the bolts with the nuts on top.
B) Apply torque on the bolts. Select torque value that corresponds with the pipe size and model designation of the unit shown on table 1 for model B1000-B1300 and table 2 for B2000-B2300. When tightening, it is recommended that the nut is turned rather than the bolt head and that the bolts are cross-torqued until the required torque has been achieved to obtain an even pressure on the structural insulation.
C) Ensure that the bolts are properly cross-torqued by checking the spacing “b” between the ears to be approximately the same (see Figure B).
Note: These units are designed for specific axia and laterall travel. Prior to tightening of the bolts, the unit may require cold setting. See figure A – A1 & B. For recommended axial and lateral cold setting instruction for this unit.
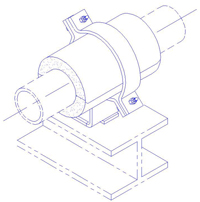
Completed Assembly
Model B1000 – B1300
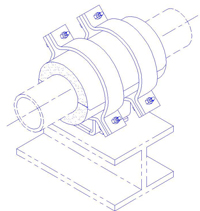
Completed Assembly
Model B2000 – B2300
Recommended Axial and Lateral Cold Settings
A) Axial cold setting: Position base assembly such that after the support has moved, the center line of the strap ( marked by the center line) approximately matches the center line of the slide pad.
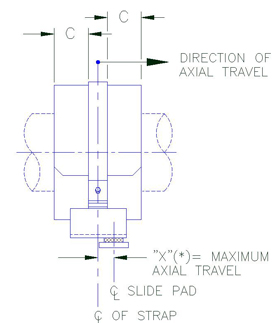
Axial Cold Setting
Model B1000-B1300
Figure A
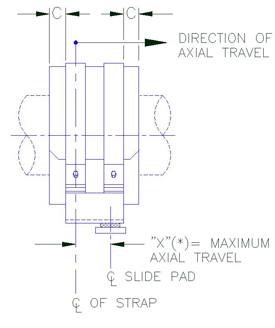
Axial Cold Setting
Model B2000-B2300
Figure A1
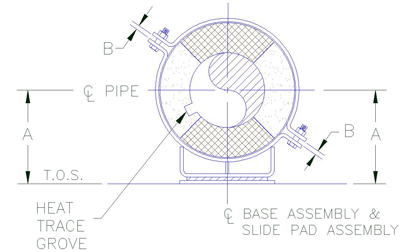
Lateral Cold Setting
Figure B
B) Lateral cold setting: Match the center of the base assembly over the center of the slide pad assembly (Figure B)
Table 1
Bolt Torque & Weld Size (W) |
||||||||
Pipe Size | ||||||||
(FT-LBS) |
(FT-LBS) |
(FT-LBS) |
(FT-LBS) |
|||||
.5″ | 3-5 | 3/16″ | 3-5 | 3/16″ | 3-5 | 3/16″ | 3-5 | 3/16″ |
1″ | 3-5 | 3/16″ | 3-5 | 3/16″ | 3-5 | 3/16″ | 3-5 | 3/16″ |
1.5″ | 3-5 | 3/16″ | 3-5 | 3/16″ | 3-5 | 3/16″ | 3-5 | 3/16″ |
2″ | 3-5 | 3/16″ | 3-5 | 3/16″ | 3-5 | 3/16″ | 3-5 | 3/16″ |
2.5″ | 3-5 | 3/16″ | 3-5 | 3/16″ | 3-5 | 3/16″ | 3-5 | 3/16″ |
3″ | 3-5 | 3/16″ | 3-5 | 3/16″ | 3-5 | 3/16″ | 3-5 | 3/16″ |
3.5″ | 3-5 | 3/16″ | 3-5 | 3/16″ | 8-10 | 3/16″ | 3-5 | 3/16″ |
4″ | 4-6 | 3/16″ | 7-9 | 3/16″ | 10-12 | 3/16″ | 7-9 | 3/16″ |
5″ | 4-6 | 3/16″ | 9-11 | 3/16″ | 13-15 | 3/16″ | 9-11 | 3/16″ |
6″ | 7-9 | 1/4″ | 13-15 | 1/4″ | 20-22 | 1/4″ | 13-15 | 1/4″ |
8″ | 9-11 | 1/4″ | 18-20 | 1/4″ | 27-29 | 1/4″ | 18-20 | 1/4″ |
10″ | 10-12 | 1/4″ | 21-23 | 1/4″ | 31-33 | 1/4″ | 21-23 | 1/4″ |
12″ | 11-13 | 1/4″ | 23-25 | 1/4″ | 34-36 | 1/4″ | 23-25 | 1/4″ |
14″ | 13-15 | 1/4″ | 26-28 | 1/4″ | 39-41 | 1/4″ | 26-28 | 1/4″ |
16″ | 18-20 | 1/4″ | 36-38 | 1/4″ | 54-56 | 1/4″ | 36-38 | 1/4″ |
18″ | 20-22 | 1/4″ | 40-42 | 1/4″ | 60-62 | 1/4″ | 40-42 | 1/4″ |
20″ | 21-23 | 1/4″ | 43-45 | 1/4″ | 64-66 | 1/4″ | 43-45 | 1/4″ |
24″ | 23-25 | 1/4″ | 45-47 | 1/4″ | 68-70 | 1/4″ | 45-47 | 1/4″ |
26″ | 20-25 | 1/4″ | 50-52 | 1/4″ | 75-77 | 1/4″ | 50-52 | 1/4″ |
28″ | 27-29 | 1/4″ | 54-56 | 1/4″ | 81-83 | 1/4″ | 54-56 | 1/4″ |
30″ | 39-41 | 1/4″ | 78-80 | 1/4″ | 118-120 | 1/4″ | 78-80 | 1/4″ |
32″ | 41-43 | 1/4″ | 82-84 | 1/4″ | 123-125 | 1/4″ | 82-84 | 1/4″ |
36″ | 46-48 | 1/4″ | 92-94 | 1/4″ | *138-140 | 1/4″ | 92-94 | 1/4″ |
42″ | 52-54 | 1/4″ | 103-105 | 1/4″ | *155-160 | 1/4″ | 103-105 | 1/4″ |
48″ | 58-60 | 1/4″ | 118-120 | 1/4″ | *175-180 | 1/4″ | 118-120 | 1/4″ |
Table 2Bolt Torque & Weld Size (W) | ||||||||
Pipe Size | ||||||||
(FT-LBS) |
(FT-LBS) |
(FT-LBS) |
(FT-LBS) |
|||||
1″ | 3-5 | 3/16″ | 3-5 | 3/16″ | 3-5 | 3/16″ | 3-5 | 3/16″ |
1.5″ | 3-5 | 3/16″ | 3-5 | 3/16″ | 3-5 | 3/16″ | 3-5 | 3/16″ |
2″ | 3-5 | 3/16″ | 3-5 | 3/16″ | 3-5 | 3/16″ | 3-5 | 3/16″ |
2.5″ | 3-5 | 3/16″ | 3-5 | 3/16″ | 3-5 | 3/16″ | 3-5 | 3/16″ |
3″ | 3-5 | 3/16″ | 3-5 | 3/16″ | 3-5 | 3/16″ | 3-5 | 3/16″ |
3.5″ | 3-5 | 3/16″ | 3-5 | 3/16″ | 3-5 | 3/16″ | 3-5 | 3/16″ |
4″ | 3-5 | 3/16″ | 3-5 | 3/16″ | 3-5 | 3/16″ | 3-5 | 3/16″ |
5″ | 3-5 | 3/16″ | 3-5 | 3/16″ | 6-8 | 3/16″ | 3-5 | 3/16″ |
6″ | 3-5 | 1/4″ | 7-9 | 1/4″ | 10-12 | 1/4″ | 7-9 | 1/4″ |
8″ | 3-5 | 1/4″ | 9-11 | 1/4″ | 13-15 | 1/4″ | 9-11 | 1/4″ |
10″ | 5-7 | 1/4″ | 10-12 | 1/4″ | 16-18 | 1/4″ | 10-12 | 1/4″ |
12″ | 6-8 | 1/4″ | 11-13 | 1/4″ | 17-19 | 1/4″ | 11-13 | 1/4″ |
14″ | 7-9 | 1/4″ | 13-15 | 1/4″ | 20-22 | 1/4″ | 13-15 | 1/4″ |
16″ | 9-11 | 1/4″ | 18-20 | 1/4″ | 27-29 | 1/4″ | 18-20 | 1/4″ |
18″ | 10-12 | 1/4″ | 20-22 | 1/4″ | 30-32 | 1/4″ | 20-22 | 1/4″ |
20″ | 11-13 | 1/4″ | 21-23 | 1/4″ | 32-34 | 1/4″ | 21-23 | 1/4″ |
24″ | 11-13 | 1/4″ | 23-25 | 1/4″ | 34-36 | 1/4″ | 23-25 | 1/4″ |
26″ | 13-15 | 1/4″ | 25-27 | 1/4″ | 38-40 | 1/4″ | 25-27 | 1/4″ |
28″ | 13-15 | 1/4″ | 27-29 | 1/4″ | 40-42 | 1/4″ | 27-29 | 1/4″ |
30″ | 20-22 | 1/4″ | 39-41 | 1/4″ | 59-61 | 1/4″ | 39-41 | 1/4″ |
32″ | 21-23 | 1/4″ | 41-43 | 1/4″ | 62-64 | 1/4″ | 41-43 | 1/4″ |
36″ | 23-25 | 1/4″ | 46-48 | 1/4″ | 69-71 | 1/4″ | 46-48 | 1/4″ |
42″ | 26-28 | 1/4″ | 52-54 | 1/4″ | 78-80 | 1/4″ | 50-52 | 1/4″ |